Fillers and Impact Resistance
Impact Resistance
This term tells us how much energy the part can take before it breaks or shatters due to sudden, high-speed impact. The term impact strength is often used but that should be avoided because strength means force whereas impact resistance is an energy. If you’ve been getting this wrong for years, don’t worry, many of the top experts do too. Impact resistance is important for motorcycle helmets, toys, shatter-proof windows and many other applications.
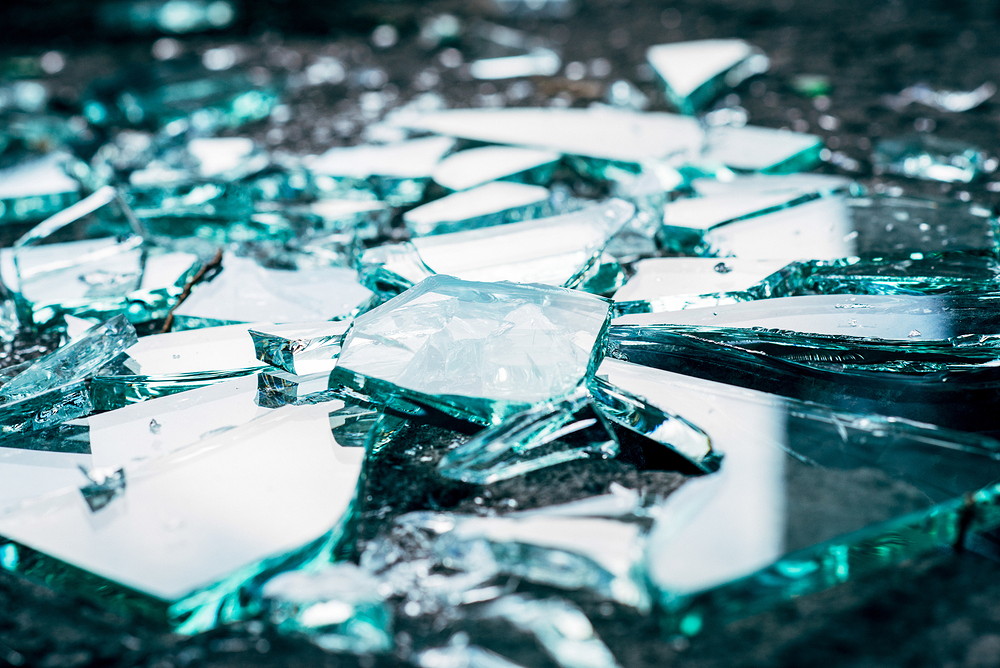
What filler property affects impact?
When a plastic part is subjected to impact, a crack can form and that crack quickly grows and the part fails. Filler particles are stress concentrators, so cracks tend to form around the filler particles. The bigger the particles, the worse the problem is, so large particles lead to low impact resistance, brittle materials. Small, well-dispersed filler particles give highly impact resistant polymer composites.
Most of the time, people choose filler grades based on the average particle size, i.e. the D50 number. However, the average particle size has nothing to do with most properties. Take for example impact resistance. It is only the few largest particles that matter. They are the largest stress concentrators and it is those particles that lead to crack initiation. When selecting a filler grade for maximum impact we need to look at the D98 number instead because that tells us how big the very largest particles are. As a rule of thumb, in thermoplastics and thermosets, particles above 20 microns or so should be avoided. Also, the best results are obtained only when the filler particles are perfectly dispersed. Often people select fine particles or nanoparticles and are surprised when they get terrible impact results. The reason is that very small particles do not disperse well, so you end up with huge agglomerates that weaken the plastic, just as larger particles do. So remember, impact does not depend on the particle size shown on the filler data sheet from the supplier, it depends on the actual size of particles and agglomerates in your final composite material.
Recommendation
Calcium carbonate is commonly chosen when impact resistance is key. Small, round particles are not significant stress-concentrators, so impact resistance is maintained. Dolomite is similar and may also be used. Surface treated grades e.g. stearic acid coated types improve performance, especially when combined with good dispersion achieved via a twin-screw extruder or similar. As mentioned, grades should be selected based on the D98 value which reflects the coarsest particles and not the mean particle size.
A typical calcium carbonate would have 2 microns mean size, a 10 micron topcoat and stearic acid coating to give best impact results. When such a product is added at 10-20 weight % to a brittle polymer like PP homopolymer or uPVC, the impact resistance will actually improve quite substantially. The reason is the upon impact the filler particles debond creating a foam so now instead of one catastrophic crack, there are thousands of tiny voids that can blunt any cracks before they become too large. When such a calcium carbonate is added to a softer, more ductile polymer like PP copolymer or plasticized PVC then there will be a loss of impact resistance because the polymer, which can absorb impact energy and convert it to heat, is being replaced by a hard, brittle mineral which cannot.
Conclusions
This gives an introduction to selecting the right mineral filler when impact resistance is your primary concern. However, there are many other factors to consider. For example, do you care what colour the filler is? Are there other requirements? The list goes on. Furthermore, all grades are not created equal. For example, particle shape also has a significant effect on many properties of the composite material.
Contact us to describe your exact needs, so we can make a recommendation based on your particular circumstances.