Fillers and Strength
Strength
Strength of polymers is commonly referred to as strength at yield or ultimate strength (also known as strength at break). Break strength is easy to understand, it is simply the amount of force required to break the plastic part. Strength at yield on the other hand, means the amount of force required to deform the part such that is doesn’t spring back to its original size and shape when the force is removed.
Tensile strength means that the plastic is tested by stretching it and flexural strength implies that the force is applied to bend the part. Compressive strength means that the part is squashed, but that is much less common as a test method. The method chosen should be the one that most accurately reflects the forces the part will be exposed to in your application.
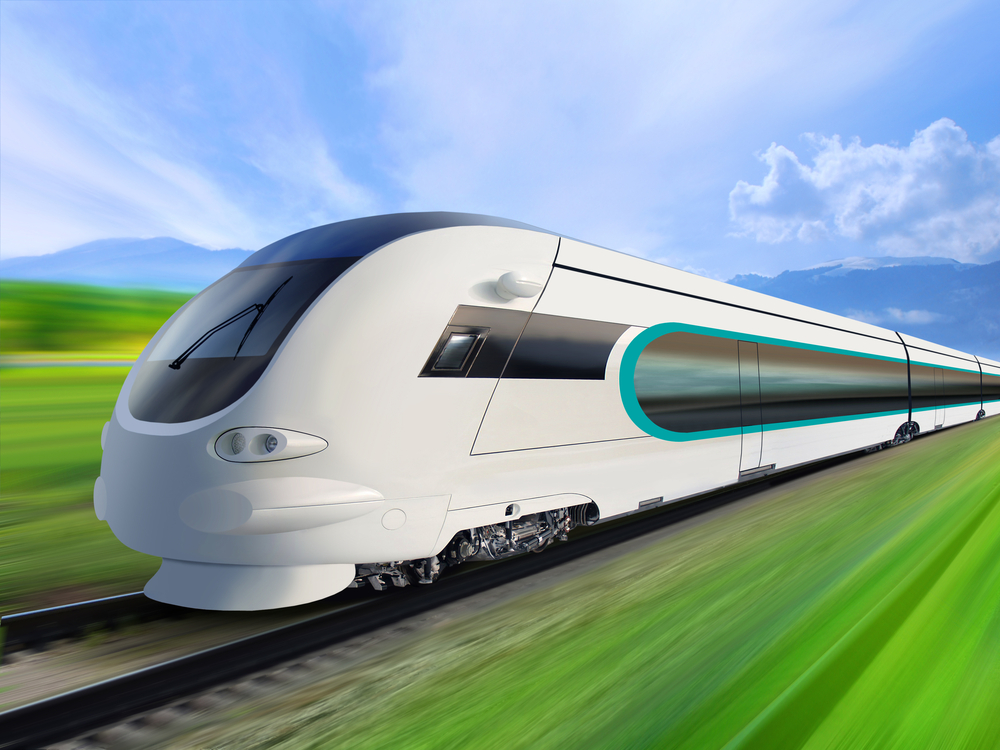
What filler property affects strength?
Round and cubic fillers like calcium carbonate, silica or glass beads slightly reduce strength. These fillers have very low aspect ratio meaning the longest dimension of the particle divided by the shortest dimension. For example, spheres have an aspect ratio of 1 and are therefore not so effective at increasing strength.
Fillers with medium aspect ratio include talc, kaolin and wollastonite. These are good at increasing strength due to their aspect ratio, which is typically in the range 10:1 to 40:1
High aspect ratio fillers are typified by glass fiber, wet ground mica, nanoclay and graphene. These are highly effective at increasing the strength of plastic.
Recommendation
Sometimes the goal is the lowest possible cost. In that case, ground calcium carbonate is the most common choice. Dolomite is similar and may also be used.
If the goal is a moderate improvement in strength without too much added cost, then talc is typically chosen. Dry ground mica, wollastonite and kaolin clay may also be considered depending on the other demands on the material.
When the goal is maximum strength, then chopped glass fiber is the first choice in most instances. Long glass fiber, carbon fiber or even Kevlar fiber can be used when cost is no object.
Conclusions
This gives an introduction to selecting the right mineral filler when strength is your primary concern. However, there are many other factors to consider. For example, do you care what colour the filler is? Are there impact resistance requirements? The list goes on.
Furthermore, all grades are not created equal. For example, particle size has a significant effect on many properties of the composite material. Similarly, the aspect ratio of different grades of any given mineral has a strong effect on properties. It is not enough to select mica, one needs to choose the correct size and aspect ratio too.
Contact us to describe your exact needs, so we can make a recommendation based on your particular circumstances.