Fillers and Elongation to Break
Elongation to Break
This term tells us how much the part can be stretched before it snaps. It is usually expressed as a percentage, so, for example cable jackets need very high elongation to break, often 400% or more. When I first heard that, it didn’t make sense to me because no-one is going to stretch a cable to several times its original length. The reason cable jackets need to be flexible with a high elongation to break is because they are often bent in a tight angle when installed. Think of a cable bent at a sharp 90° angle, the outside of the jacket is severely stretched and that is why elongation to break is important.
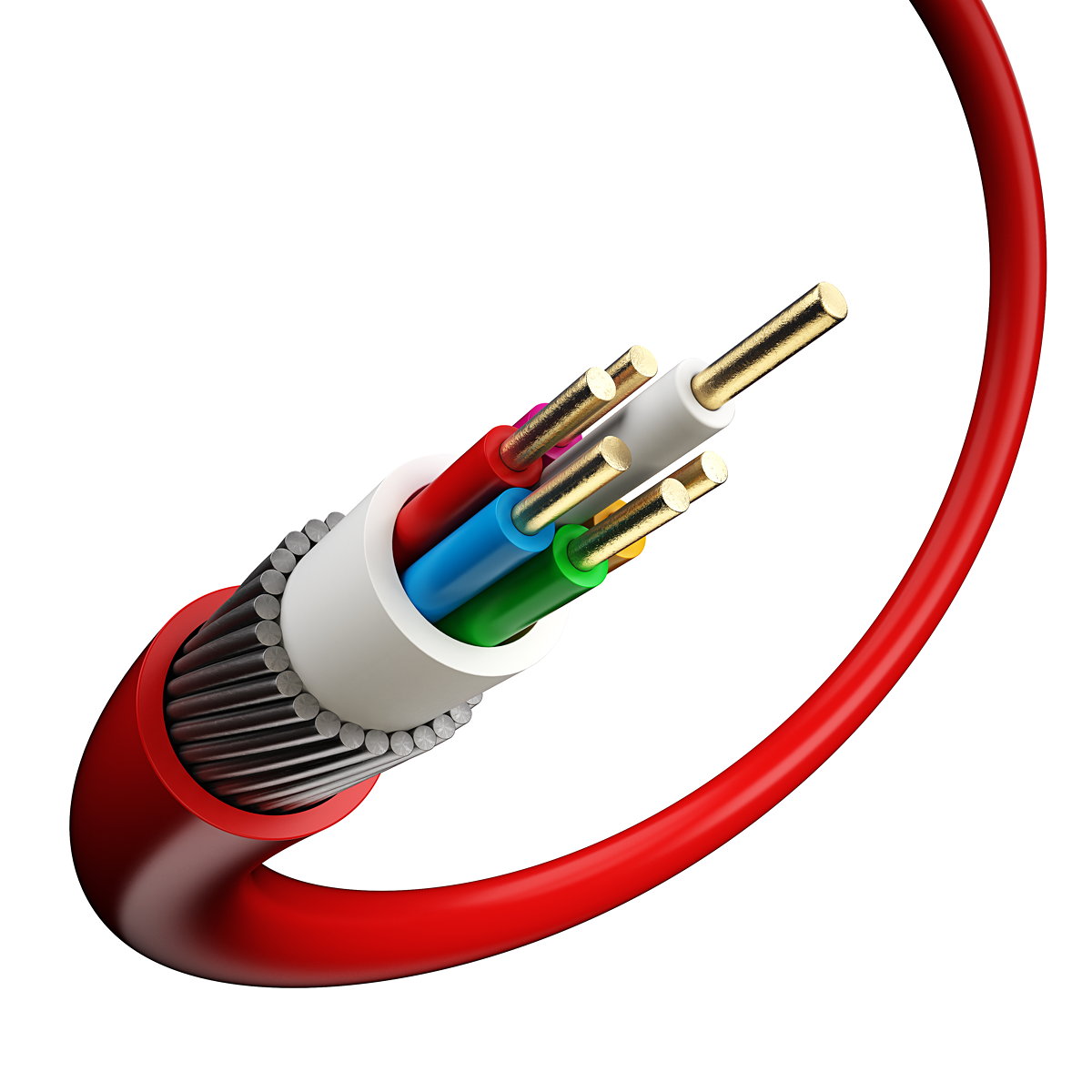
What filler property affects elongation?
We learned that stiffness and strength depend on the shape of the mineral filler particles, that is the aspect ratio determines those properties. Perhaps surprisingly, elongation depends on a different filler property. When a plastic part is stretched, eventually a crack will form and that crack quickly grows and the part fails. Filler particles are stress concentrators, so cracks tend to form around the filler particles. The bigger the particles, the worse the problem is, so large particles lead to low elongation to break, brittle materials. Small, well-dispersed filler particles give high elongation to break, i.e. ductile polymer composites.
Most of the time, people choose filler grades based on the average particle size, i.e. the D50 number. However, the average particle size has nothing to do with most properties. Take for example elongation to break. It is only the few largest particles that matter. They are the largest stress concentrators and it is those particles that lead to crack initiation. When selecting a filler grade for maximum elongation to break we need to look at the D98 number instead because that tells us how big the very largest particles are. As a rule of thumb, in thermoplastics and thermosets, particles above 20 microns or so should be avoided. Also, the best results are obtained only when the filler particles are perfectly dispersed. Often people select fine particles or nanoparticles and are surprised when they get terrible elongation to break. The reason is that very small particles do not disperse well, so you end up with huge agglomerates that weaken the plastic just as larger particles do.
Recommendation
Sometimes the goal is to retain elongation at the lowest possible cost. In that case, ground calcium carbonate is the most common choice. Dolomite is similar and may also be used. Surface treated grades e.g. stearic acid coated types improve performance, especially when combined with good dispersion achieved via a twin-screw extruder or similar. As mentioned, grades should be selected based on the D98 value which reflects the coarsest particles and not the mean particle size.
Conclusions
This gives an introduction to selecting the right mineral filler when elongation is your primary concern. However, there are many other factors to consider. For example, do you care what colour the filler is? Are there impact resistance requirements? The list goes on. Furthermore, all grades are not created equal. For example, particle shape also has a significant effect on many properties of the composite material.
Contact us to describe your exact needs, so we can make a recommendation based on your particular circumstances.