Fillers and Gloss / Matte
Gloss / Matte
This term related to how the plastic surface looks. In technical terms, it is a measurement of the percentage of light that reflects off the surface. Typically it is measured at an angle of 20, 60 or 85°. Low angles, e.g. 20° give lower gloss values and are more sensitive to gloss changes. Smooth surfaces act like a mirror resulting in high gloss. Conversely, rough, textured surfaces scatter the incoming light beam in different directions, so that most of it does not reach the detector. That results in a low gloss measurement. Sometimes gloss is adjusted for purely cosmetic reasons but in other cases, such as a car dashboard, low gloss is needed to prevent sunlight reflecting and temporarily blinding the driver.
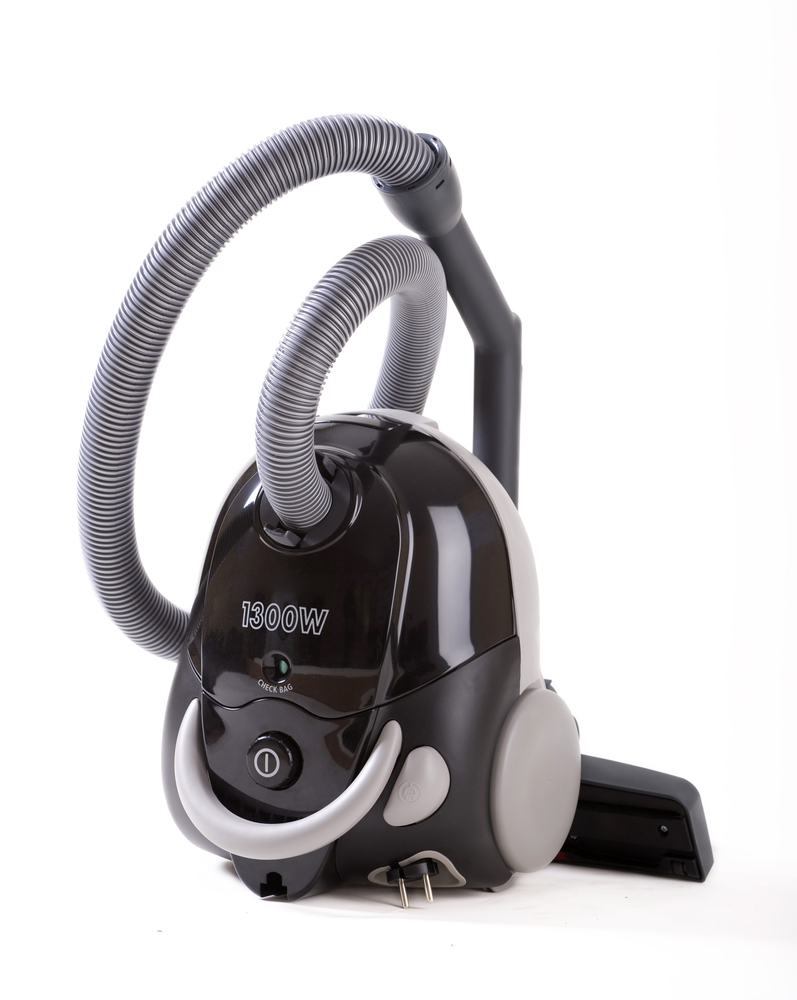
What filler property affects gloss?
Surface roughness is usually adjusted by adding texture to the injection mold or calendar roller. When it comes to fillers, it is found that high gloss is achieved by using finer filler particles that are well dispersed. Of course, lower filler loadings also help retain high gloss. When a matte surface is needed, then larger filler particles are selected and the loading level is increased substantially.
Recommendation
Sometimes the goal is to retain elongation at the lowest possible cost. In that case, ground calcium carbonate is the most common choice. Dolomite is similar and may also be used. Surface treated grades e.g. stearic acid coated types improve performance, especially when combined with good dispersion achieved via a twin-screw extruder or similar. As mentioned, grades should be selected based on the D98 value which reflects the coarsest particles and not the mean particle size.
Conclusions
This gives an introduction to selecting the right mineral filler when elongation is your primary concern. However, there are many other factors to consider. For example, do you care what colour the filler is? Are there impact resistance requirements? The list goes on. Furthermore, all grades are not created equal. For example, particle shape also has a significant effect on many properties of the composite material.
Contact us to describe your exact needs, so we can make a recommendation based on your particular circumstances.