Functional Fillers
Introduction
Functional fillers are widely used in plastics and the trend is for ever increasing use of fillers driven by several factors. Firstly, fillers allow for plastic materials with a much wider range of properties including properties not normally associated with plastics, such as high electrical conductivity or thermal conductivity. Functional fillers can be used to reinforce plastics, for example fillers like talc and glass fiber have allowed polypropylene to compete successfully in the engineering polymers market. Almost all plastics are made from petroleum feedstock and the price of plastics inexorably increases as abundance of oil and gas declines. In contrast, mineral fillers are abundant and filler prices climb at a much slower pace, with the consequence that filled plastics become more commercially attractive year after year. The same resins are available to all but by understanding fillers and other additives well, one can craft formulations that outperform.
While there are whole books devoted to this subject, it can be rather hard to learn from them because they contain too much information and it is spread over hundreds of pages. I know because I own most of them and have helped write a few. The books are great if you are already an expert and are looking for more detail on a narrow topic, but are of little help for anyone else. Therefore, this article will give an overview of the whole topic, in a concise manner, with links to more detailed pages on individual topics. Furthermore, it is written from a practical standpoint, with an intentional avoidance of equations and other theoretical nonsense, which does nothing to improve understanding of materials or how to design them.
A brief overview
Composites are made from two or more different materials and their properties are usually somewhere in between those of the starting materials. So, if I add hard mineral particles to a soft rubber, the hardness of the rubber will increase. That is a very useful tool for making materials which have properties in between those of the pure materials. For example, adding a functional filler to polypropylene (PP) can give a composite with mechanical properties similar to unfilled nylon, but less expensive than nylon. For most properties, the linear rule of mixtures applies. That is a fancy way of saying that the properties of the composite are the weighted average of the properties of the components. So, if we were to mix 50 volume % PP and 50 volume % calcium carbonate, the stiffness of the filled PP we just made would be roughly halfway in between the modulus of the polymer and the filler. Note that every single property, including cost, depends on the volume percentage of each component and not the weight percentage. It is essential to grasp that. If I mix 50 weight % calcium carbonate and 50 weight % PP, the density of the composite is not the average of the densities of the starting materials. That surprises just about everyone, including me when I got started.
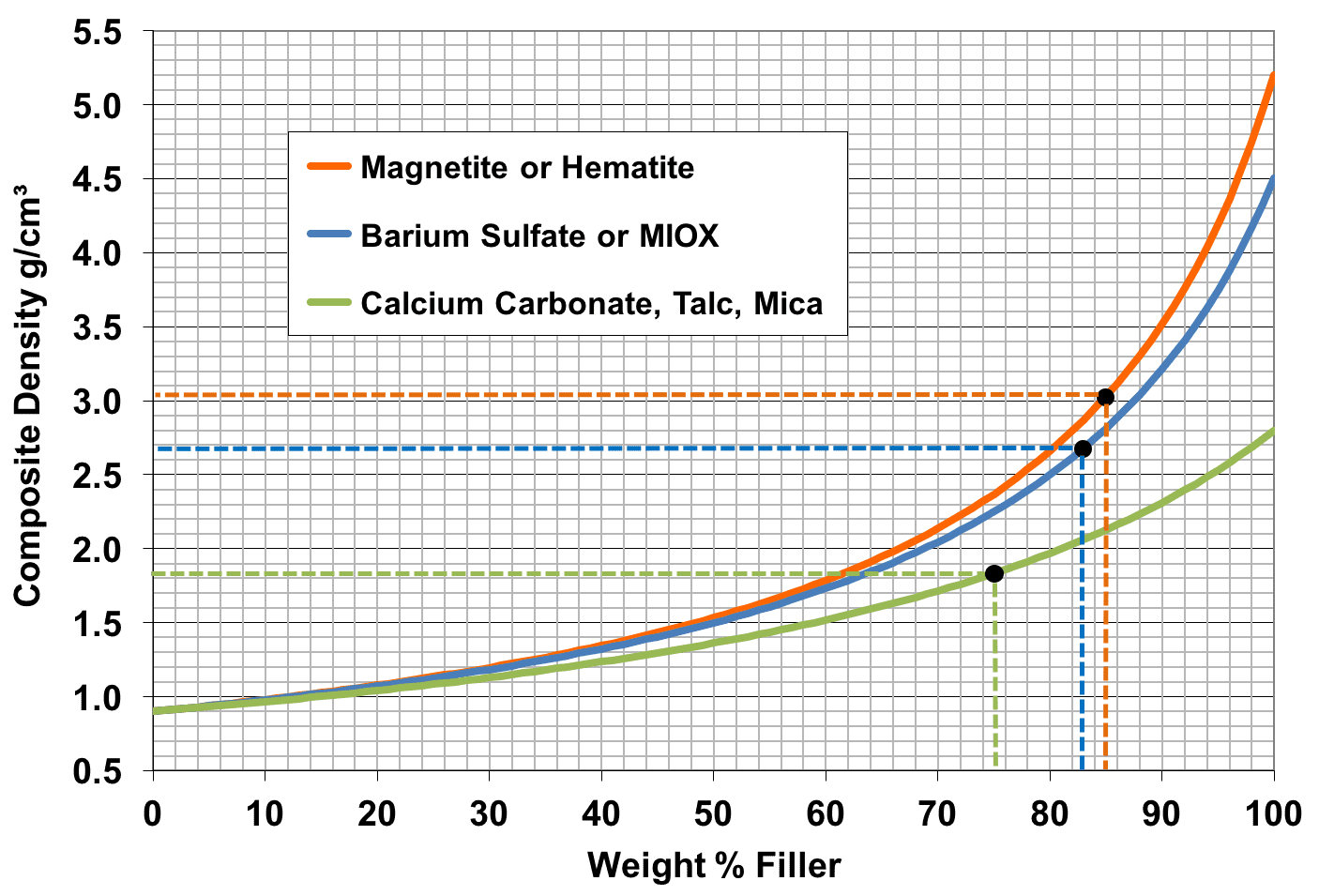
Unfortunately, just about every graph you will ever see will be plotted with weight % filler on the x-axis because in practice one weighs out the ingredients for compounding. A plot of composites modulus (stiffness) against weight % filler is a curve and scientists spend lots of time finding equations to fit such curves. A plot of modulus against the volume percentage of filler gives a straight line. Straight lines mean less headaches, less superfluous equations and most importantly, they make interpolation and extrapolation easier. What do I mean by that? It means that instead of running experiments for zero, 10, 20, 30 and 40 weight % filler, you only need to do zero and 30%, for example and draw a straight line between the points and out to 40%. That means a giant saving in time and money so you can make new formulations faster and more cheaply. Note that one still measures out the filler by weight but then plots the results with volume % filler on the x-axis. This information although key and also obvious when you think about it, is not pointed out anywhere so you can waste ten years of your career before it becomes clear. It happened to me, so l am happy to spare you the same fate.
There is no ideal polymer, nor ideal filler. Composites are about compromises and to make the best trade-offs requires a firm grasp of the properties of the starting materials and how the ingredients interact with each other. One can however, list some typical desirable properties of functional fillers.
• Low cost
• Readily available world-wide
• Safe
• Pure
• Chemically unreactive / inert
• Stiffer and stronger than the polymer
• Non abrasive
• Colorless (appears white in powder form)
Following from that, it may come as no surprise that the most popular mineral fillers are calcium carbonate, talc, kaolin, mica and glass. There are many types of specialty filler available but these common types are a good starting point for understanding structure – property relationships and because they are so important from an economic standpoint. They are the go-to additives in many cases. Before looking at each in turn, it must first be said that it is misleading, almost to the point of being meaningless, to describe a filler by its chemistry because in most cases, the chemistry has no effect on the composite. So, what is important? The main properties of a functional filler that matter for mechanical properties are:
• Particle size distribution
• Particle shape
• Surface area
Therefore, let’s consider each briefly.
Particle size distribution
When people talk about particle size, they normally focus on the average particle, size known as the D50. It is commonly specified on datasheets from the filler suppliers. Ironically, it has almost nothing to do with the properties of a composite. Instead it turns out that the smallest and largest particles in the distribution dominate properties. The D98 gives an indication about the size of the largest particles. Those acts as flaws in the polymer, weakening it and providing a place for a crack to start and grow. In laypersons terms, think of felling a tree. What do you do to fell a tree? You put sharp notch in it to provide a weak spot where forces concentrate making it far easier to make the tree fall. Filler particles act in much the same way and the larger the particles, the worse the problem. As a rule of thumb, particles over about 10-20 microns start to seriously affect the impact resistance and elongation to break of a composite. Coarser particles also lead to poor surface finish, i.e. low gloss. That may be useful if you want a matt surface but usually, it is not desirable.
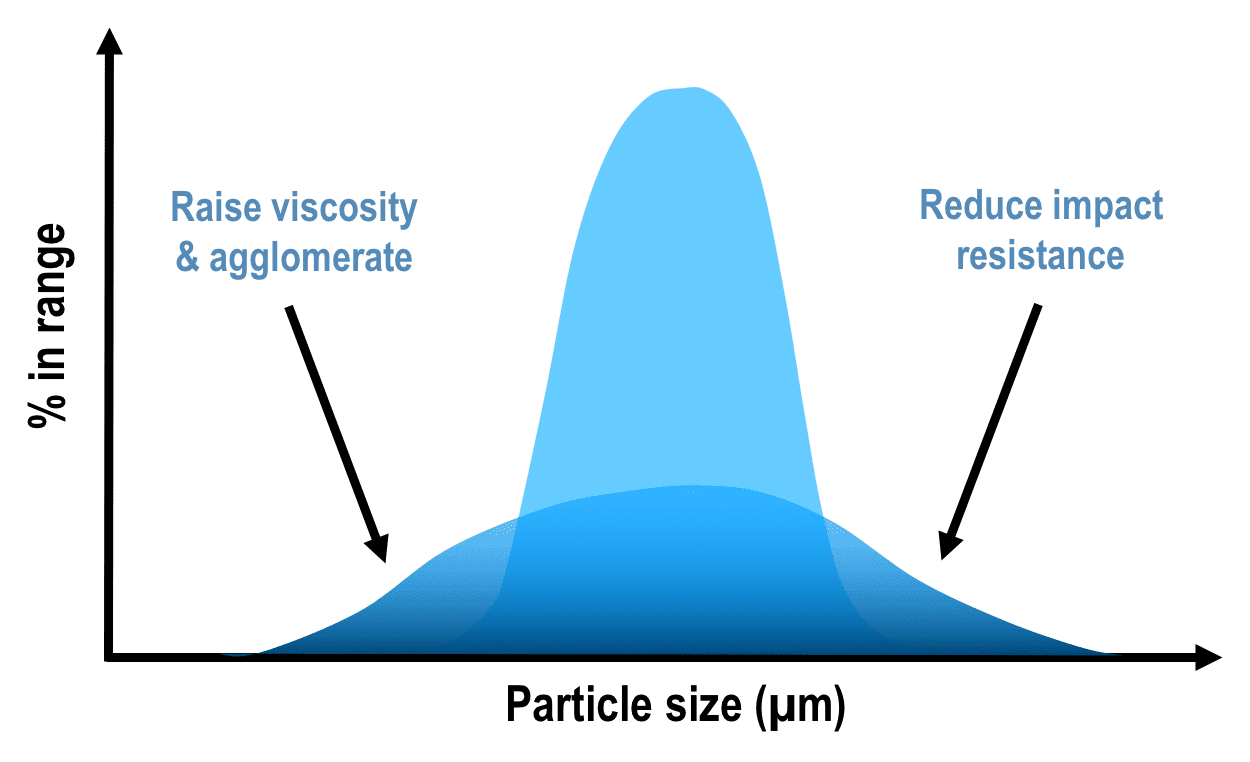
Particle shape
The D10 relates to the smallest particles in the distribution curve. Small particles are better in theory and that is one reason for all the talk about nanocomposites. In practice however, very fine particles cause problems. They tend to stick together, causing large agglomerates that act just like larger particles and ruin impact resistance, elongation to break and gloss. Small particles also lead to high viscosity because of the forces holding them to each other. That lowers productivity and limits how much of them you can add before the material becomes unprocessable.
Particles can have many shapes, but for simplicity, we can put them in three groups.
Round or cubic particles where calcium carbonate (calcite) or glass spheres are typical examples. That shape of particle increases stiffness somewhat, decreases strength slightly and has least effect on impact resistance and elongation to break. An advantage is that properties are altered equally in all three directions (x, y & z) and there is no tendency for warpage.
Needle shaped particle and fibers typified by wollastonite and glass fiber, can reinforce plastics if the aspect ratio is high enough and if they are well bonded to the surrounding polymer. The key property is aspect ratio, which simply means the largest dimension of the particle divided by the smallest dimension. So, for a needle 10 microns long and 1 micron wide, the aspect ratio is 10:1. Higher aspect ratio means better reinforcement. What does reinforcement mean exactly? It’s a term used a lot, but rarely does anyone say what it means. The best definition I have seen is that a reinforcement increases both stiffness and strength.
Platy particles for example talc and mica, can also reinforce and the higher the aspect ratio, the more effective they are. They reinforce along both of the long dimensions of the plate, whereas a fiber only reinforces along its one long dimension. So, in that sense, plates are more effective than fibers of equivalent aspect ratio. Plates also have the benefit of giving barrier properties, that is gasses and liquids cannot easily penetrate through plastics filled with high aspect ratio platy fillers. In recent years, high aspect ratio talc and mica have gained traction due to high reinforcement effectiveness. Platy fillers also lead to more isotropic shrinkage, i.e. less warpage and are often added to fiber filled composites to alleviate the high warpage that fibrous reinforcements can create.
Aspect ratio gives reinforcement but usually poor impact resistance and lower elongation to break. This implies that fibers and plates act as flaws. The reason is that to have high aspect ratio, you need to have one (for fibers) or two (for plates) long dimension(s). That long dimension is likely to be over the 10-20 micron limit where stress concentrations are high, facilitating crack initiation and failure. There is one more important point to make about aspect ratio. The aspect ratio that matters is not the one from the datasheet which describes the as-supplied powder. What does matter is the aspect ratio of the particles inside the final composite material because that is what affects mechanical properties, barrier and so on. It is therefore vital to ensure the particles are not broken down, decreasing aspect ratio, during handling and compounding. The more aspect ratio that can be preserved, the better the final properties.
Surface area
The surface of a filler particle is what interacts with other particles and with the surrounding polymer. The more surface there is, the more such interaction we can expect. So, what does that mean in practical terms? High surface area means more tendency for agglomeration, creating higher viscosity and more work is needed to keep the particles separated. On the other hand, high surface area means more contact with the polymer giving improved adhesion between the two. If we think of everyday life, we sand a surface before applying glue because sanding increases the surface area and thereby improves adhesion. The same principle applies to composites. Increased adhesion between filler and polymer primarily affects the tensile and flexural strength. Strength increases because, when there is good adhesion, the forces on the polymer can be transferred to the filler particles. When adhesion is poor, then the particles debond and cannot bear load, so the strength of the composite suffers. Surprisingly, good adhesion is not always desirable.
Nanocomposites
It may seem premature to be talking about nanocomposites here but we know enough already to understand why they are so appealing and also why they haven’t taken off. Montmorillonite nanoclay plates are so thin (~1nm) that the platelet long dimension can be under 1 micron and yet, the aspect ratio can still be very high. That means you should be able to get great stiffness and strength but retain good impact and elongation because that long dimension is too short to be a stress concentrator. The same thinking applies to tubular clay nanoparticles like halloysite. However, as we now know, small, high surface area particles agglomerate severely to give large particles and poor properties. That has been the plight of nanocomposites with decades spent trying to get ideal dispersion. Even when a method is found to get good dispersion, it is too slow or expensive to be commercially attractive.
Here is a table that summarizes all of that. Now that we have built a foundation over just a few pages, we can move on to the many other aspects that contribute to the behavior of polymer composites.
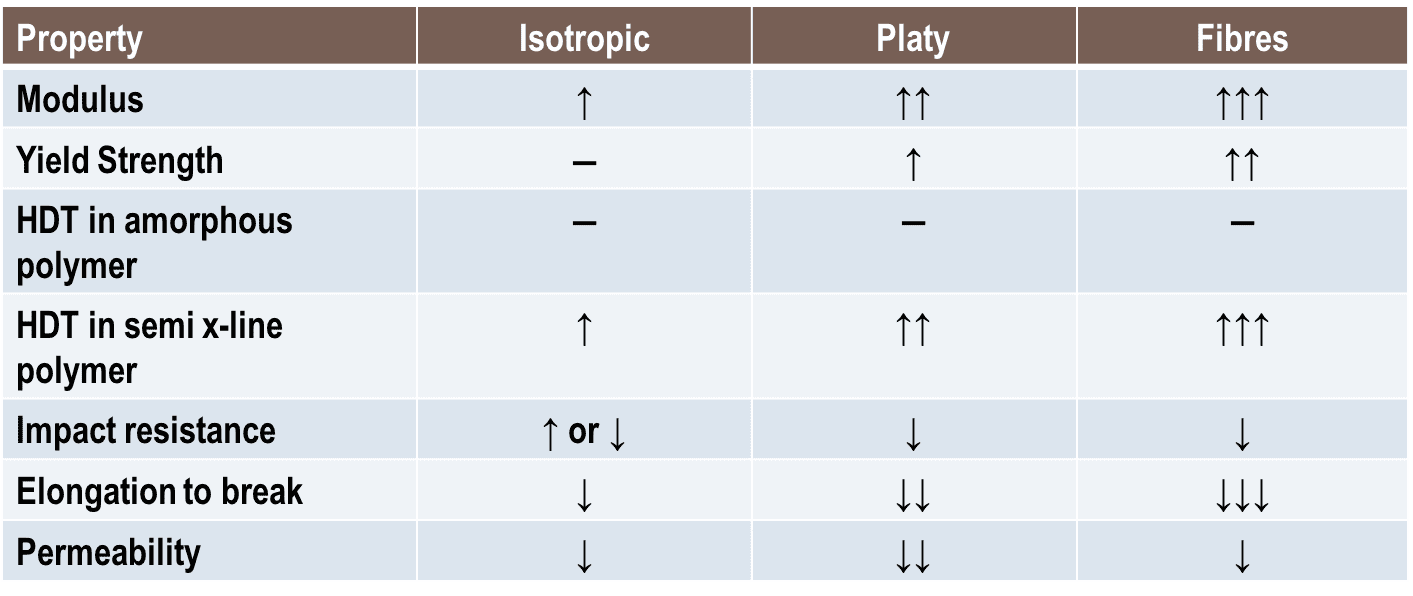
Common functional fillers
There are many different fillers and each one has a unique property set. This section gives an introduction to each filler, its properties and main application.
Calcium Carbonate – CaCO3
Calcium carbonate is a soft, inexpensive filler, that is readily available world-wide. High purity calcium carbonate is colorless but appears white in powder form due to light scattering. Different particle sizes are available as are surface treatments. For many applications, it is the obvious choice, particularly in the less expensive polymers like PE, PP and PVC where it can improve stiffness, retain strength and improve impact resistance while lowering materials costs. Ground calcium carbonate is used predominantly but finer, submicron precipitated grades are available. If reinforcement of the polymer is not required, then calcium carbonate is often the first choice.
Talc – Mg3Si4O10(OH)2
Talc is a very soft mineral that is colorless when pure and appears white in powder form. The particles are generally platy so talc does reinforce when the aspect ratio is high enough. It is used extensively for applications needing good mechanicals with low cost and low weight. Automotive use is popular with the newer high aspect ratio (HAR) talc grades gaining traction. Talc is also a good nucleating agent, helping polymers like PP and nylon to crystallize faster which speeds part production.
Kaolinite – Al2Si2O5(OH)4
Kaolinite clay is a member of the Kaolin family of aluminosilicates. It is a soft white or tan powder where the particles are platy in shape. Similar to talc in that it can reinforce when the aspect ratio is high enough. Kaolinite is widely available, inert and inexpensive.
Wollastonite – CaSiO3
Wollastonite appears as a white powder with high hardness (Mohs 4.5) compared to other common fillers. The hardness makes it good for scratch resistance particularly in PP for automotive use. It is the most common fibrous mineral reinforcement and has replaced asbestos since its demise. It is not as effective as the best reinforcements because aspect ratio tends to be lower than for HAR talc or mica. Unlike other silicates, wollastonite does not have good resistance to acids and bases.
Mica muscovite – KAl2(Si3AlO10)(OH)2 and phlogopite – KMg3(AlSi3O10)(OH)2
Muscovite is the most common form of mica and is white or off white. Phlogopite is darker in color but has much high temperature stability. Both types behave similarly in polymers assuming comparable particle size and aspect ratio. They can be highly reinforcing when milled to give high aspect ratio platelets. Sound damping and good electrical properties are other desirable attributes. The picture below shows large, approximately 3 cm2 plates of phlogopite as mined.
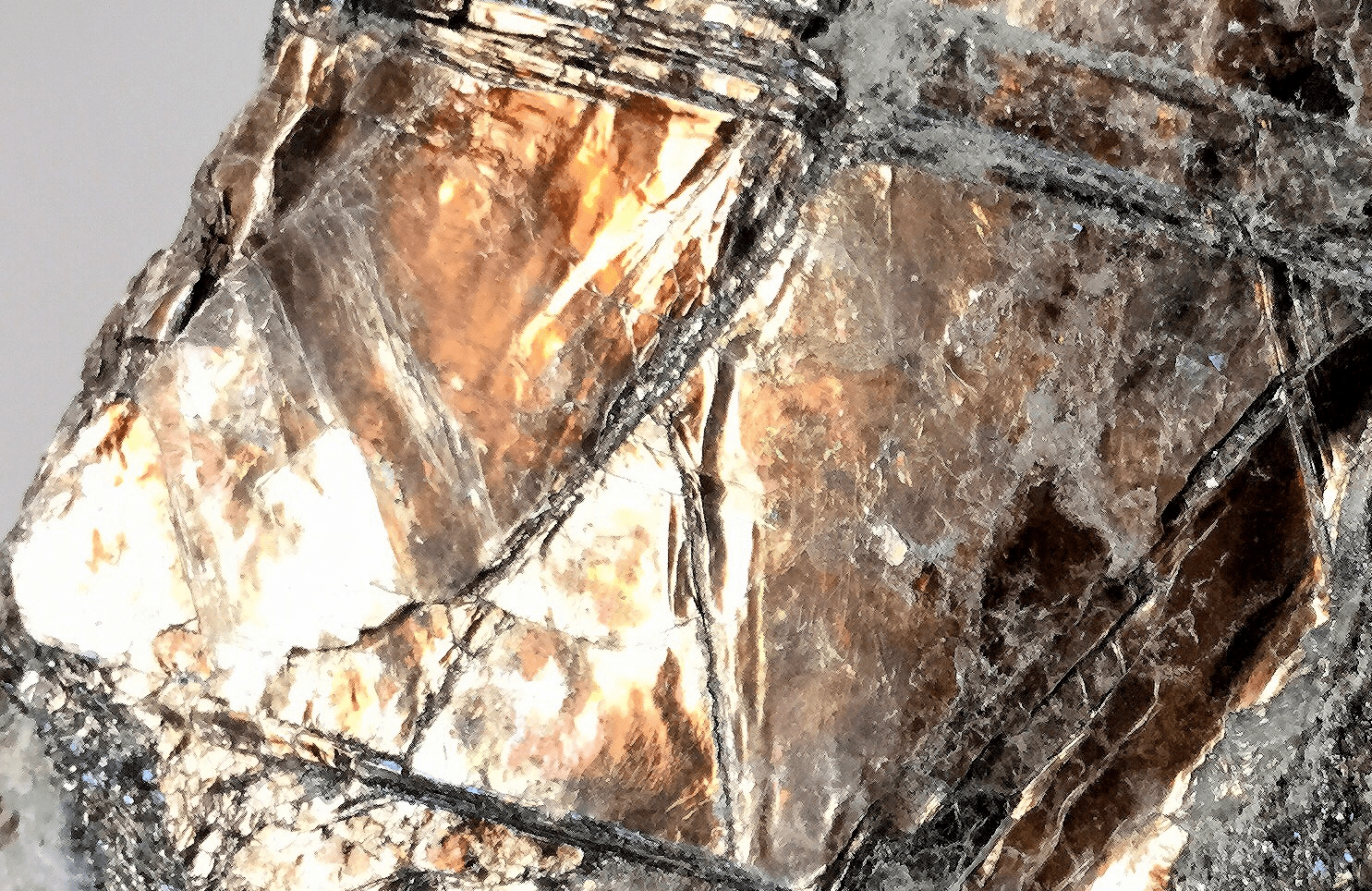
Glass beads – SiO2
Glass beads are used to reduce warpage, particularly in glass fiber filled polymers. They promote good flow and surface finish. They are therefore particularly popular in the engineering polymers like nylon and PBT or thermosets like phenolic resins and epoxies. Hollow types are used when density reduction is sought.
Glass fiber
There are difference glass types but E glass is most commonly used in polymers. As for all other fillers, the degree of reinforcement depends on the aspect ratio. In the case of glass fiber, high aspect ratio or even continuous fibers, can be used, creating very effective reinforcement. Surface treatments are commonly employed to protect the fibers and to improve adhesion to the polymer under harsh conditions such as high humidity or elevated temperature. Glass fibers are hard and special care must be taken to protect the processing equipment from wear and the glass fibers from breakage.
Flame retardant fillers
Aluminium trihydrate (ATH) – Al(OH)3
ATH is the most common flame retardant filler. It decomposes when heated above 180-200°C at which point it absorbs heat and releases water to quench the flame. The low decomposition temperature is suitable for polymers that are processed at under 200°C like PE, EVA and EBA. However, it cannot be used in PP and most other polymers because the ATH decomposes during compounding. ATH does occur naturally as the mineral Gibbsite but most FR grades are purer, synthetic precipitated products. Surface treatments are often because high loadings, in the region of 60 weight % are needed to get a good flame retardant rating. The surface treatment helps reduce the viscosity in such highly filled compounds. Large amounts are used in synthetic marble countertops (so-called solid surfaces) and those grades are usually surface treated with an organosilane coupling agent to improve bonding to the acrylic matrix polymer.
Magnesium hydroxide (MDH) – Mg(OH)2
Magnesium hydroxide is selected for PP and other polymers that are processed at higher temperature because it has higher thermal stability than ATH. Endothermic (heat absorbing) decomposition starts at 300°C whereupon water is released to combat the fire in much the same way as in the case of ATH. MDH does occur naturally as the mineral brucite but deposits are relatively rare and the natural product suffers from impurities and sub-optimal particle shape for the high loadings needed. Thus synthetic grades are more popular, although far more costly, than either brucite or precipitated ATH. Coated grades are available where dispersant types lower processing viscosity and coupling agents improve bonding and thereby the strength of the composite. Surface treatments can also improve wet electrical performance.
Huntite / Hydromagnesite blends – Mg3Ca(CO3)4 / Mg5(CO3)4(OH)2·4H2O
Huntite and hydromagnesite occur, almost invariably, as mixtures in nature. Commercial deposits are rare. Mainly in Greece and more recently in Turkey. The hydromagesite starts to decompose between 220°C (open air) and 250°C (under pressure in an extruder), which is high enough so that it can be used as a flame in polypropylene. It also finds use in PE, EVA and EBA. The hydromagnesite gives off water and absorbs heat, much like ATH and MDH do. In contrast, the huntite decomposes above 400°C, absorbing heat but liberating carbon dioxide. As a natural mineral product, it is inherently less expensive than precipitated ATH or MDH. Hydromagnesite has low aspect ratio but huntite is a medium aspect ratio platy material which alters polymer melt flow behavior and provides some reinforcement.
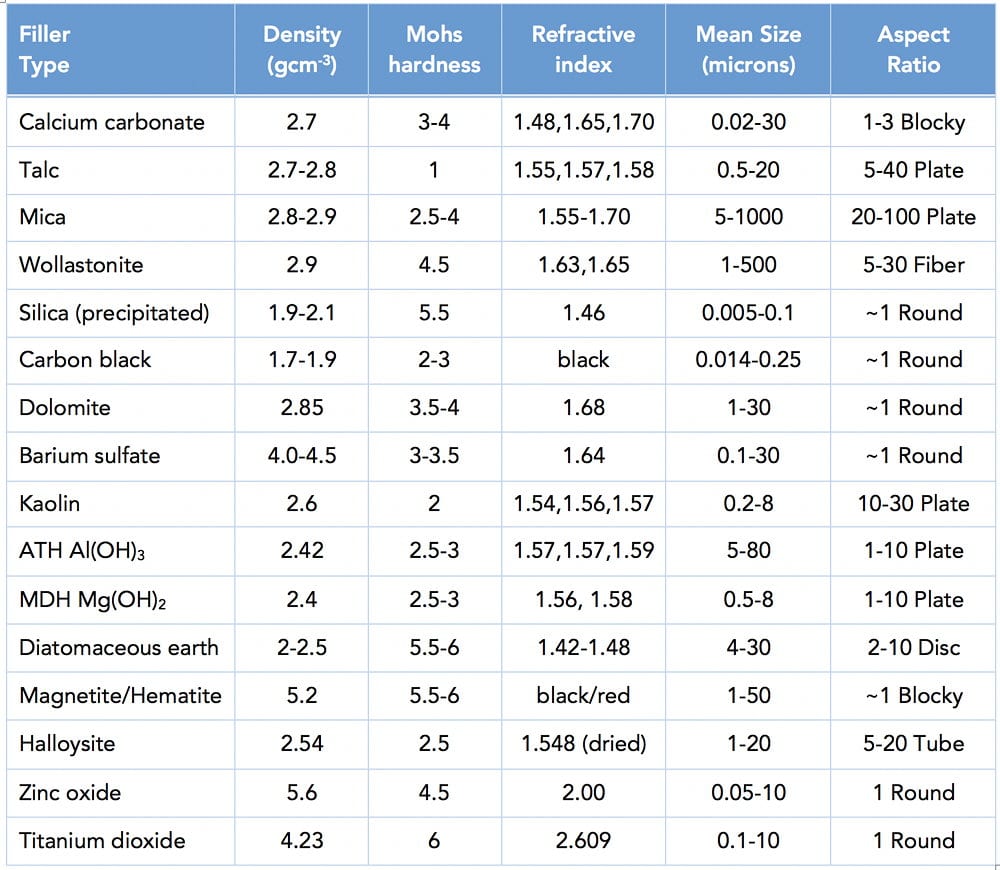
Specialty functional fillers
The fillers covered above are of most importance in terms of volume used but many other types are selected to achieve particular effects.
Barium Sulfate (Barite or Blanc Fixe) – BaSO4
White in powder form, it occurs naturally as the mineral barite or the corresponding synthetic version is referred to as Blanc Fixe. The two main attributes are high density (4.0-4.5 gcm-3) depending on purity and radio opacity. It is therefore added to polymers to make them heavy, e.g. for sound damping or to make them x-ray visible for implants to give on example. It is highly unreactive (inert). The particles are blocky in shape and therefore non reinforcing.
Magnetite – Fe3O4
A black lustrous powder with unusual properties. Often used for its high density (5.2 gcm-3 for pure grades). It also has high electrical conductivity and quite high electrical conductivity. It is x-ray opaque and can be used to block radiation. Magnetite is non reinforcing due to the low aspect ratio of the particles. The many unusual properties are detailed here (magnetite page) and in an encyclopedia chapter I authored.
Hematite – Fe2O3
Coarse, pure hematite is a shiny gunmetal grey colour but when ground finer, below about 5 microns in size, the particles change colour and are rust red. This red colour is used a a pigment and is the basis for rouge used in cosmetics. Hematite has the same density (5.2 gcm-3 for pure grades) as magnetite and is highly effective in sound deadening applications but is normally less expensive making it an attractive alternative to magnetite. Hematite heats rapidly when exposed to microwaves and can reach 400°C in 2 minutes. Hematite absorbs radar which can be useful in stealth applications. Hematite has very high thermal conductivity (12.5 W/m.K) which is 4-5 times higher than typical mineral fillers. This leads to very low cycle times when molding hematite-filled plastics. Until recently, pure hematite was not available as a filler for plastics but in 2017 Arctic Minerals launched DenzFlex™ hematite as a functional filler. Other information can be found on the hematite page.
Tungsten – W
Tungsten is a pure elemental metal used for very high density composites such as lead replacement. Tungsten itself has a density of 19.25 gcm-3 and the name comes from Swedish where “tung” means heavy and “sten” means stone. It is far more expensive that barium sulfate or magnetite and also much harder causing machine wear.
Dolomite – CaCO3·MgCO3
Dolomite is similar to calcium carbonate (calcite) but with some subtle differences. It is also a soft white powder but it is much rarer to find deposits of sufficient whiteness for polymer applications. It is slightly harder and denser than calcite and has greater resistance to attack by acids. Note that it is not a mixture of calcium carbonate and magnesium carbonate but rather a distinct mineral.
Magnesium oxysulfate (MOS) fiber – 5Mg(OH)2·MgSO4·3H2O
Although this product has been manufactured and used for several decades, it is not at all well known. With a fiber diameter of 0.5 microns and mean length of 15 microns, the aspect ratio is approximately 30:1 as supplied. After processing into polymer that is reduced but is still enough to provide reinforcement in PP and other polymers. Strength is improved using MOS fibers but modulus and HDT are very good. Stearic acid has been used successfully as a dispersant and silane grafted PP can be used as a coupling agent to boost strength. Although fibers with these dimensions normally have asbestiform behaviour, MOS fiber is soluble, non-persistent and therefore considered safe.
Halloysite – Al2Si2O5(OH)4
Halloysite is an aluminosilicate and member of the Kaolin group of minerals. It has identical chemistry to kaolinite but instead of platy particles, the silicate sheets are rolled up in a scroll-like fashion to create nanotubes. These are typically 50nm in diameter and a few microns long to give an aspect ratio of 10-20:1 and thus moderate reinforcement. Although many potential applications have been postulated, commercialization in polymers has been very slow to take off. More information on halloysite can be found on a dedicated page (halloysite page).
Polyhedral oligomeric silsesquioxanes
These are technically molecules that look like particles and have therefore been described as “molicles”. The center of the molecule is a silica-like cage which is surrounded by organic groups which impart solubility. This means it is possible to add rigidity but with perfect compatibility and the option to chemically bond to the matrix polymer. Applications are starting to take off in the last couple of years. More information on these unique additives can be found on a separate page.